
1.Fabric dyeing/Finishing process
Cotton, linen, and other fabrics cannot be used as woven fabrics.
They can be shipped as fabrics only after undergoing dyeing processes to add color, control texture, stabilize shrinkage, and so on.
Dyeing and processing in the Bicchu and Bingo regions began with indigo dyeing, which was the mainstay of dyeing for student uniforms, working clothes, and other items requiring functionality and fastness. In addition, since the history of weaving began with cotton cultivation, the region excels in natural fibers such as cotton and hemp, as well as medium-weight fabrics among cotton x polyester fibers.
As for the dyes used, while reactive dyes are the mainstream in other regions, we can handle a variety of dyes such as indigo, selenium, sulfide, reactive dyes, pigment dyes, and natural dyes.
Of course, we use only dyes, auxiliaries, and other chemicals that meet ZDHC® 2.0 standards.
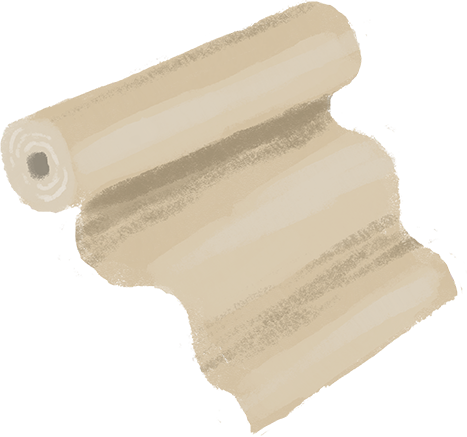
2.Denim fabric finishing process
Finishing is necessary even if the woven fabric is not dyed, such as denim or raw fabric.
It is important to stabilize shrinkage and distortion while bringing out the best of the woven denim.
In addition, indigo dye develops a unique flavor as it ages, and vintage processing can be used to express this change from the beginning.
In recent years, stretch denim has become more and more common, so we often add a special finishing process that makes the twill stand out and makes the finished product stand out.
Kurashiki Dyeing uses only chemicals that meet the ZDHC® 2.0 standards for the finishing process.
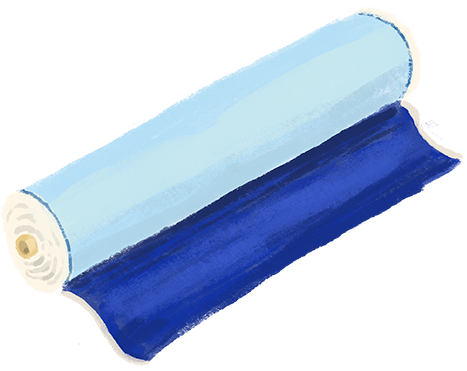
3.Dyeing processing of products
Dyeing process to dye sewn products as they are. Sewing with white fabrics and dyeing them in various colors is once again attracting attention because it reduces wasted inventory.
All chemical dyes such as sulfide dyes, Suren dyes, and reactive dyes are all used only safe ones that meet ZDHC® 2.0 standards.
In many cases, the unique wrinkle and texture of product dyeing is required. Not only plain dyeing, which dyes uniformly, but also various techniques such as tie-dyeing and blotting can be used.
Inkjet printing can be used to print on the product itself to create a variety of patterns.
Inkjet printing is also highly valued for the fact that it does not require a printing plate and does not use water.
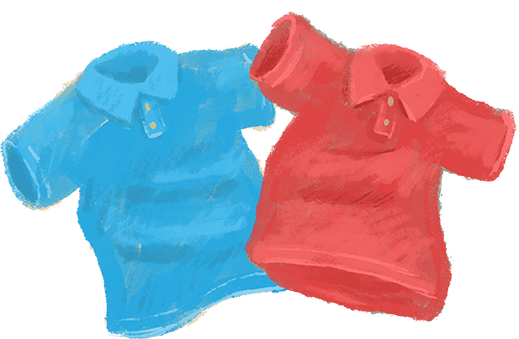
4.Jeans washing process
Kurashiki is also a production center of jeans. About the same time as the birth of domestic jeans, a washing process was developed to make brand new jeans softer and easier to wear. At that time, jeans shrank a lot after being washed once. So, by washing and shrinking them beforehand, it became easier to choose the size.
Various methods have been developed to reproduce the texture of old clothes, such as chemical wash using chemicals, stone wash, and bio-wash, but these methods also placed a heavy burden on the workers. In recent years, the way of working has changed with the advancement of mechanization, such as processing with laser beams and robot arms.
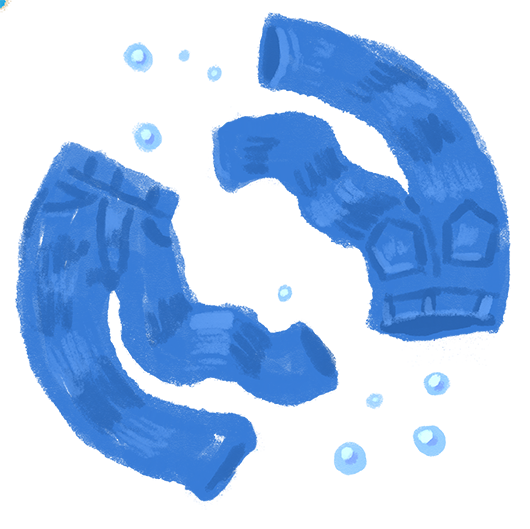
5.Fabric bleaching/Coloring of prints
Printing is done on plain dyed or bleached fabric using a rotary textile printing machine. Up to 12 colors can be used.
We specialize in indigo bleaching prints, in which patterns are expressed by removing colors from plain dyed fabrics using indigo dyes.
In addition to indigo, the factory also produces many camouflage patterns, a staple of casual wear.
(Joined KURASHIKIZOME® in April 2023)
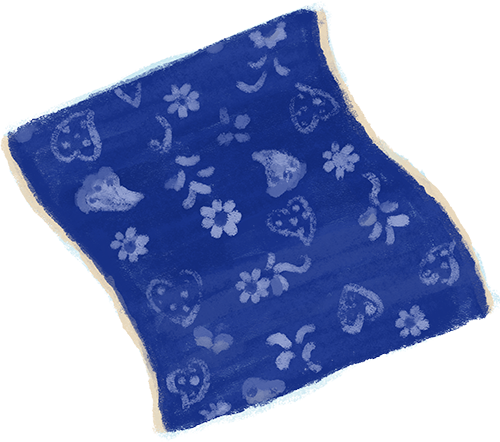