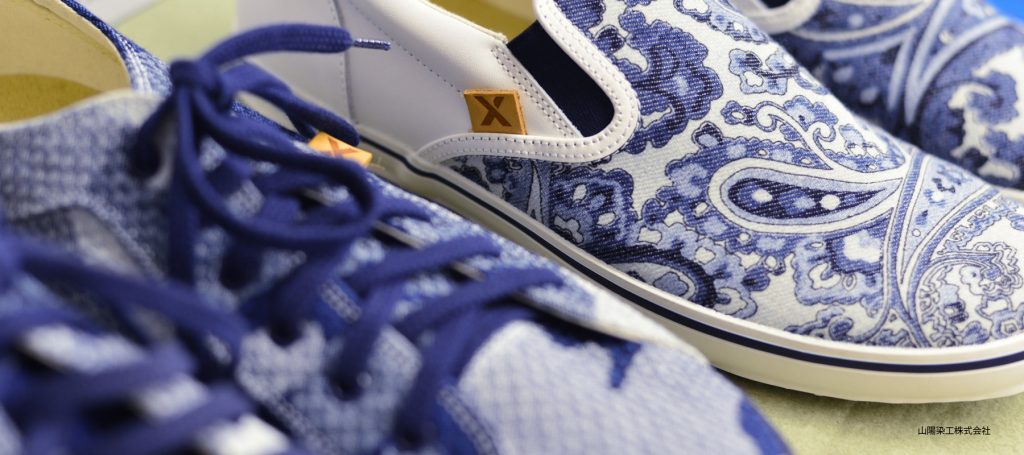
Member participating in “KURASHIKIZOME®”
SANYO SENKO Co.,Ltd.
SANYO SENKO was founded in Fukuyama City, Hiroshima Prefecture in 1925 and will soon celebrate its 100th anniversary. It is well known as a major dyeing and finishing factory in Japan, but it is also a huge group company with six non-textile affiliated companies in addition to Chugoku Boshoku, a weaving company. SANYO SENKO has participated in KURASHIKIZOME® as the Kojima Factory of SANYO SENKO in Kojima, but the closure of the Kojima Factory at the end of March 2011 was the occasion for the new head office to join the KURASHIKIZOME® group. The participation of SANYO SENKO Works, headquartered in Fukuyama City, gave KURASHIKIZOME® the opportunity to expand outside of Okayama Prefecture. We interviewed Mr. Masaki Takeyari, General Manager of the Sales Department.
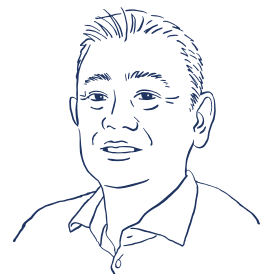
SANYO SENKO Co.,Ltd
Sales Department
Masaki Takeyari
Passing on the technique of indigo stencil dyeing that began with Bingo kasuri
Okayama and Hiroshima are known as denim production areas. The area is unique in its ability to produce everything from denim fabrics to finished products in an integrated production system. SANYO SENKO is in charge of dyeing and processing in the production area, and the major difference between Sanyo Dyeing and other companies in the production area is that we can dye fabrics with indigo dyes first. Secondly, we can print patterns. Another major difference between our company and other companies in the region is that we excel in a technique called “Bassen,” in which colors are removed from the dyed fabric to match the pattern.
As you know, denim fabric is dyed with indigo dye at the thread stage to make it dark blue before weaving. The reason for this lies in the origin of the company’s foundation.
This area was originally a production area of Bingo Kasuri, which turned into a denim fabric production area. Bingo kasuri is a fabric for kimono woven with indigo-dyed threads in dark blue, so the company turned to indigo-dyed denim fabric production. Under these circumstances, the founder thought that fabric dyeing would be more efficient than yarn dyeing, and researched fabric dyeing techniques and equipment for manufacturing Bingo Kasuri. Bingo kasuri is characterized by a white pattern on a navy blue background, and he studied the technique of bleaching in order to remove the white pattern after dyeing. Indigo fabric dyeing and Bassen are our ancestral business, and we intend to pass them on to the next generation with great care.
Indigo fabric dyeing and printing technology as a weapon!
We are often asked how indigo fabric dyeing differs from regular denim, and there are advantages and disadvantages.
The advantage is that, compared to yarn-dyed denim fabrics, it is possible to produce small-lot production, starting with a single roll, to put it in the extreme. Also, while most denim fabrics are made of medium- to thick-weight fabrics, fabric dyeing can be used to dye thin shirt fabrics and linen fabrics. In fact, there are many orders for indigo dyeing of shirt fabrics and linen fabrics. The disadvantage is that the color tends to fade even more easily than regular denim fabrics. We hope that apparel and brands will understand both the advantages and disadvantages and use both regular denim fabric and indigo fabric dyeing.
Since huge washing and drying facilities are required, Sanyo Dyeing is probably the only factory in Japan capable of indigo dyeing of raw fabrics.
In addition, Sanyo Dyeing is the only factory that can print patterns, which is rare among denim fabric production areas in Fukuyama and Okayama, so it is able to separate itself from other dyeing and processing plants.
Our great advantage is that we can not only do precise printing using a rotary textile printing machine that can use up to 12 colors, but also combine Bassen with Discharge, such as extraction dyeing, which requires high technology. We have a huge amount of pattern data accumulated to date, and some of our standard patterns, such as camouflage patterns, have been repeated for many years.
A corporate culture that allows us to take on the challenges of both overseas expansion and original products
Until about nine years ago, SANYO SENKO had been a dyeing and finishing company that took on orders from the work clothes industry, orders from major fabric trading companies, orders from the bedding industry, and tobes for the Middle East. However, the company’s prospects were not good with only wage processing, so Kojima Factory was brought in as a group company with the aim of developing sales channels for casual wear. The company also began selling its own original fabrics.
Unfortunately, Kojima Factory was closed at the end of March, but the know-how and casual wear sales channels developed there will be utilized at the main factory in the future. The strength of our original fabric sales lies in our integrated production system, from raw fabric to dyeing, which we have developed together with our group company, Chugoku Boshoku.
We began this new initiative about 9 years ago, and have developed sales channels for casual wear, but domestic demand continues to shift to smaller lots. We have been exhibiting at Milano Unica in Italy for the past five years with the aim of developing overseas sales channels. In February 2011, we exhibited jointly with Shinohara Textile in Fukuyama, and we are beginning to feel a positive response.
As a new business, we started “BASSEN WORKS,” an original product brand specializing in denim fabrics and Indigo slip-dyeing about 3 years ago, and in April this year, we provided “Momoiro Clover Z” with an originally designed G-jan as a costume for their live performance. Our corporate culture encourages us to take on new challenges, such as exhibiting overseas and branding our products, so we would like to be even more bold and proactive in our endeavors.