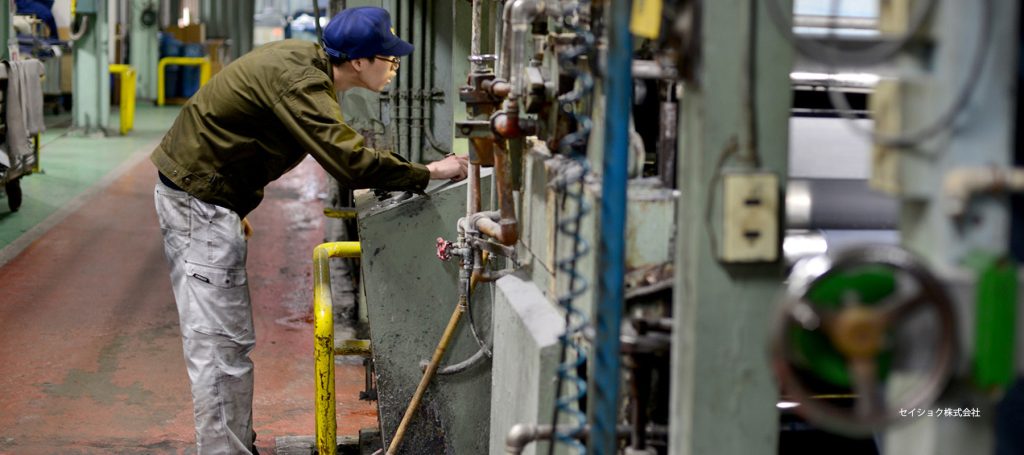
Member participating in “KURASHIKIZOME®”
Seisyoku Co.,Ltd.
In the vast factory, dyeing and processing machines of various sizes are lined up, and craftsmen wearing caps with the “SEISHOKU” logo on them are moving briskly among them. We interviewed President Himei at Seishoku’s Okayama Plant, where the saw-toothed roof that lets in just the right amount of sunlight evokes a sense of history.
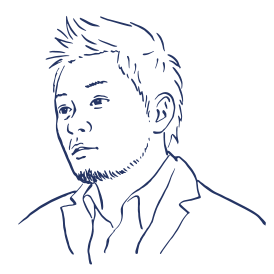
Seishoku Co.,Ltd
CEO
Akira Himei
Born in Tone-gun, Gunma
Established as a textile factory in 1880
The history of “Seishoku” is quite old. The company was founded in 1880 as a weaving factory. From there, the company gradually expanded its operations to other processes and began spinning cotton yarns in 1925. With this, an integrated production system from spinning to weaving was established. In 1942, the company acquired a bleaching and dyeing factory and began to engage in dyeing and processing. In 1945, the company began manufacturing (weaving) thick fabrics for uniforms. In 1960, we also developed dyeing of artificial leather. The company’s main business was weaving and dyeing for working wear for a long time, but it has now discontinued weaving and is operating as a dyeing and finishing factory.
The dyeing and finishing plant in Okayama City is the largest in western Japan, covering 23,300 square meters and with a monthly production capacity of 2 million meters. Although it is no longer in use, there used to be a company dormitory on the site. Currently, the plant has a flexible production system to meet the volume of orders, and has updated its facilities to match the environment, such as updating boilers for this purpose.
The main dyeing method for working wear fabrics is continuous dyeing, which is suitable for dyeing cotton and cotton/polyester fabrics used for working wear. Continuous dyeing lowers production costs and achieves both low-cost and large-lot production required for working wear.
Working wear is a consumable item, and it is always necessary to replace it after a certain period of time due to breakage, so the lower the cost, the more customers appreciate it. At the same time, however, manufacturers require high functionality, high colorfastness that prevents color fading, and uniformity without color irregularities or blurring, which is required for corporate uniforms. Seishoku has an established reputation for high colorfastness and uniformity cultivated through dyeing and processing for working wear, and we are confident in our ability to achieve this. We are also confident in the thorough pretreatment and color matching required to achieve this.
Does “Seishoku” attract men of science?
Although the number of young female staff has been increasing in recent years, there are many male staff members in the science field. I don’t know why (lol). Is there something brewing at Seishoku that attracts men of science?
However, dyeing and finishing is a job that combines chemistry, machinery, and computer operations, so I think the steady, steady work style of the science-oriented male staff is a good fit.
In the future, we would like to expand our business to include more sensitive work such as casual wear, so we would like to bring in more young women than ever before.
“NUNOUS🄬” a new sustainable material upcycled from waste fabrics
To be honest, textile-related factories in Japan are facing a difficult environment with the demand for small-lot production and cost reduction. Feeling anxious about surviving only as a textile-related manufacturing and processing plant, we launched the “NUNOUS🄬” business in 2018 as a new business. This was conceived as a way to reduce the waste of B- and C-textiles (fabrics that cannot be shipped because they were rejected during inspection) that inevitably arise in the processing process.
This is a patented technology that alternately layers and hardens off-standard fabrics that cannot be shipped with sugarcane-derived biofilm, which can be sliced into various thicknesses according to the intended use. It can be used not only as a material for highly designed notebook covers and card cases, but also as a material for interior decorations such as objets d’art if it is cut out thick enough.
As a result of our steady sales efforts to the architectural, interior design, and interior design industries, which are different from our traditional customers, we are finally starting to get a good response from hotels, offices, and commercial spaces that have begun to use our products as part of their interior decoration and interior design. To our delight, we have also begun to receive inquiries from European luxury brands.
Selected as one of the “100 Textile Industry Companies for the Next Generation”
In 2023, Seishoku was selected by the Ministry of Economy, Trade and Industry as one of the “100 Textile Industry Companies for the Next Generation.” In our main business, our main customers have been in the working wear industry, but in the future we would like to expand our sales channels by responding to small-lot, multi-product production for casual wear.
We have been participating in KURASHIKIZOME® to develop sustainable dyeing technologies such as natural dye dyeing, and now that we have taken over the “dusty processing” machinery and know-how from Sanyo Dyeing Kojima Factory, which closed this year, we will acquire the technology and know-how to develop small-lot processing for casual wear and high-sensitive, high-value-added processing. We would like to expand our sales channels for small-lot processing and high-sensitivity, high-value-added processing for casual wear. We are now in the process of preparing to accept machinery and equipment for this purpose at the factory.
In the future, we would like to establish a new technology unique to Seishoku by combining the working technology and sustainable dyeing technology we have cultivated up to now with a new technology for casual wear.
We hope to grow together with our customers who need our technology as one of the remaining dyeing and processing plants in Japan.