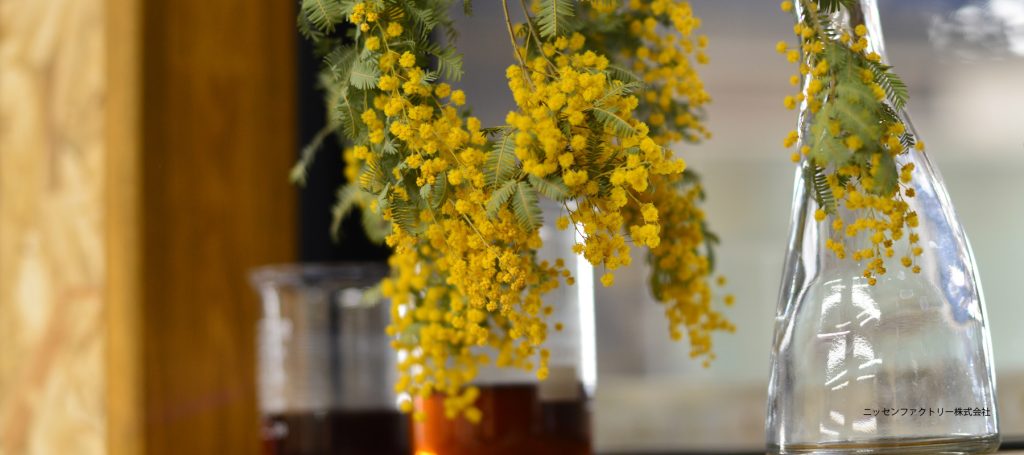
Member participating in “KURASHIKIZOME®”
Nissen Factory Co.,Ltd.
Kojima, Kurashiki City is famous for jeans, but in the Edo period, cotton was grown in the area, and dyeing of cotton, starting with indigo dyeing, also flourished. In the Edo period, cotton was grown in the area, and dyeing of cotton, starting with indigo dyeing, also flourished. The predecessor of our company was also a dyeing factory that specialized in black dyeing.” We interviewed Mr. Namba, president of Nissen Factory Corporation, a genuine craftsman who joined the company after graduating from the textile section of Okayama Prefectural Kurashiki Technical High School and took over in 2011.
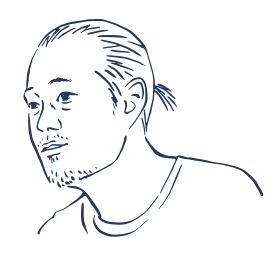
Nissen Factory Co.,Ltd
CEO
Makoto Namba
Born in Kurashiki City, Okayama
Fabric dyeing factory → To product washing process and product dyeing factory
Nissen was a dyeing factory founded just after the end of the war, and its main occupation was black dyeing using sulfide dyes, mainly for student uniforms. Later, in the era of rapid economic growth and mass production, and with the birth of domestic jeans in the 1960s, the company transformed from a fabric dyeing factory to a washing and processing plant focusing on denim products. The facilities became larger in order to handle orders from major jeans brands.
However, as jeans started to be seen as a part of fashion from around 2000, the number of jeans started to be influenced by the fashion trend and decreased.
Under such circumstances, we started to focus on product dyeing about five years ago. There is a trend to avoid excess inventory, and some brands want to use product dyeing as a concept. Product dyeing has a unique bite and worn look, and some say it has a good atmosphere.
As small-lot, high-mix production has become the norm, this spring we relocated our factory to a more compact location and renovated it to be able to make samples and handle small-lot, high-mix production.
Product dyeing that is beginning to attract attention as a sustainable product.
We wanted to dye using local materials as much as possible, so we started the KURASHIKIZOME® initiative, which includes coffee dyeing, sumi ink dyeing, and ethical dyeing using bark from lumber mills in the northern part of Okayama Prefecture. This is an application of the traditional Japanese herb and tree dyeing method, which is interesting in that the colors come out differently depending on the mordant used.
We also receive requests directly from farmers and producers, and we enjoy wondering what kind of colors we can bring out from these materials. I enjoy working with them and wonder what colors I can bring out from these materials. By taking on the challenge of using new materials, I want to emphasize the importance of “colors that can only be produced here.
For the 2024SS project, we are trying peach dyeing using selected branches from peach farmers in Kurashiki and reed dyeing using reeds from Lake Kojima. The main person in charge of herb dyeing is a female staff member who got into this job because she loves dyeing, and sometimes we even go to the fields together to get materials for dyeing.
How is this dyed? is a joy!
Since we began specializing in product dyeing, we have pursued differentiation not only in dyestuffs but also in techniques. In addition to itajime-shibori (tie-dyeing) and shibori-dyeing, which are based on traditional techniques, we have also increased the variety of tie-dyeing and blur dyeing. By combining the same techniques and changing the order, the finished product looks very different.
Inkjet printing is also doing well, so we have invested in equipment that allows us to print at five times the speed. Inkjet printing technology, which does not require water and can be processed from a single sheet, can be applied in any number of ways depending on the design. We are also actively introducing new software, which allows us to create more realistic and interesting expressions, such as converting designs into embroidery.
Our greatest strength is that we can combine dyeing, washing, and inkjet printing in-house, and when a customer who is familiar with our technology looks at a sample we have made and says, “How did you dye this? I get a hearty “gut-punch” when a customer who is familiar with our technology looks at the sample we have made and says, “How did you dye this?
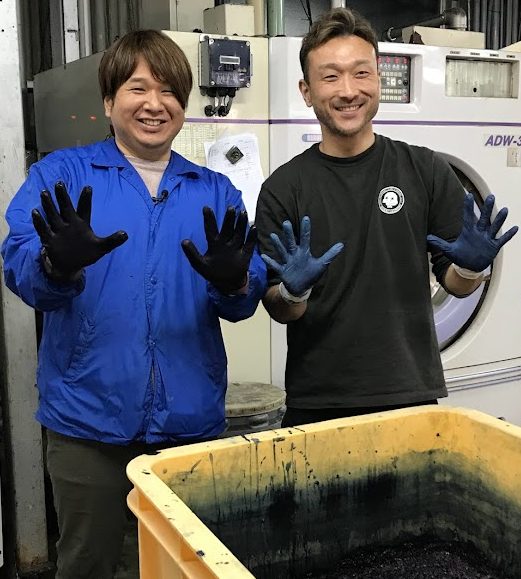
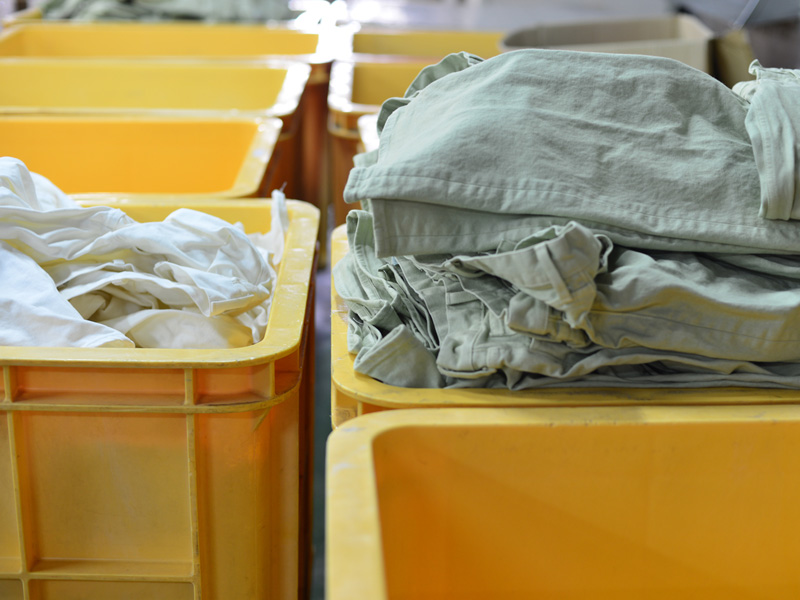
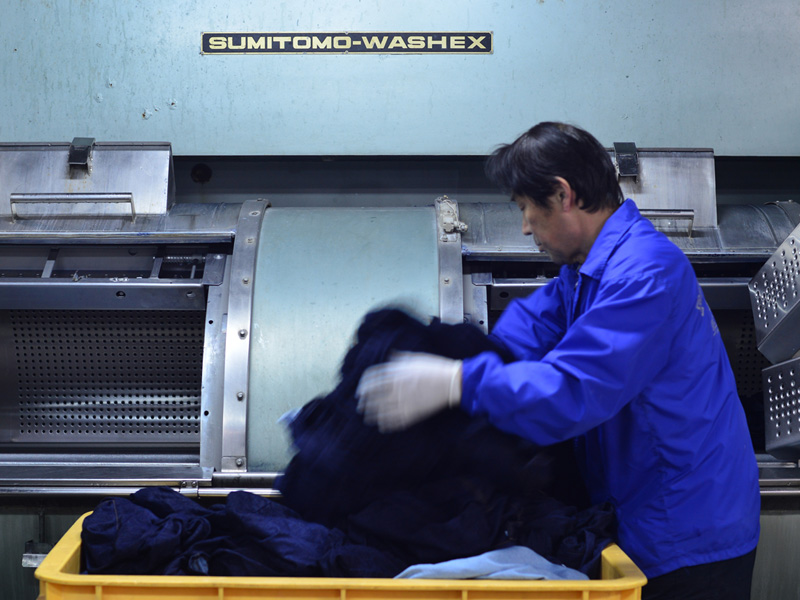
Realizing that there are unlimited possibilities for collaboration
I have been dyeing and processing for a long time and am confident in my skills and knowledge, but collaborating with another industry made me realize that there are still things I don’t know.
In a project started last year in collaboration with a cleaning factory in Asahikawa, Hokkaido, where we take customers’ old clothes and dye them indigo and charcoal gray, we were asked to do our best not to damage the clothes, unlike new clothes. So I learned a lot about rinsing temperatures and how to hang hangers. On the other hand, I was sometimes asked about dyeing knowledge and dyestuffs, so we were able to exchange knowledge, experience, and techniques.
In a sense, the KURASHIKIZOME® project is also a cooperative effort that has led to the creation of products that could not be done by a single company. I would like to continue to be proactive when there are opportunities for collaboration with partners in the same or different industries.